Texcelead associates are having decades of experience in performing rotor dynamic analysis for various rotors of machines.
The most integral components of any machinery are its rotor, bearings which support the rotor, couplings and the bearing pedestal. The characteristics and reliability of rotating machineries largely depends up on the design of rotor shafts, bearings, couplings and bearing load carrying path. In order to come with a trouble free and robust rotor design, a detailed study of rotor dynamic characteristics of rotor assembly is essential. A detailed analysis is required to understand its vibration characteristics and ensure that the design is trouble free of vibration during its intended operation.
The rotor dynamic analysis is applied to all types of rotating machineries across wide range of industries, the most common machines includes turbo-machinery, motors, centrifugal pumps, generator, air blowers supported by fluid film bearings and anti friction bearings where critical speeds or stability may be a concern
We offer excellent RDA consultancy for:
- Designing or modifying rotating machineries
- Identify the causes and solutions of poor performance in terms of vibration
- Design optimizations
- Prototype development
- Bearing co-efficient calculations
- Designing and validation to meet the various standards and codes such as API 610 etc.
To model and predicts vibration or rotor characteristics Texcelead perform the rotor dynamic analysis in the following areas:
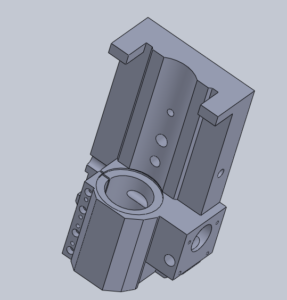
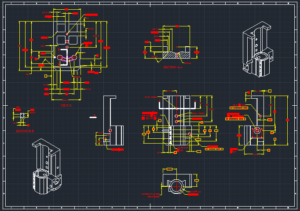
Lateral analysis
The minor radial clearance between rotating and stationary components, fatigue life, damping, and as well as the health of surrounding equipment, demand that a machine achieve excellent lateral vibration performance. This will ensure the high reliability and performance of the rotating machine.
Texcelead conducts different types of analysis to determine a machine’s lateral vibration performance, such as:
Undamped Critical Speed Analysis – Calculation of critical speeds and their sensitivity to support dynamics. In addition, the influence of unbalanced distribution, as well as component damping, can be assessed using the resulting mode shapes.
Forced Response Analysis – Unbalance response analysis provides the best estimate of critical speed location and vibration amplitudes. It is crucial for the assessment of separation margins, vibration limits, and rubbing risks.
Torsional Analysis
All the rotating machinery systems experience torsional oscillation to some degree during startup, shutdown and continuous operation as their primary requirement is to transmit power (torque). Consequently, the torsional response characteristics of rotating and reciprocating equipment should be analyzed and evaluated to ensure the system’s reliability. Severe torsional vibrations often occur with the only indication of a problem being gear noise or coupling wear. Excessive torsional vibrations can result in gear-wear, gear-tooth failures, key failures, and broken shafts in severe cases.
The torsional vibrations response of rotating machinery components is an important consideration in defining the operational reliability of a rotary equipment train. Accurate response prediction requires analysis techniques that consider all forcing functions in the system in addition to the mass-elastic properties of the shafts, coupling, gears, impellers, etc.